Like many businesses across New Zealand, manufacturers find themselves between a rock and a hard place. On the one hand, essential raw materials are in short supply. On the other, finding workers is a growing challenge, with reduced immigration for various reasons including reduced immigration owing to Covid policies. Consumer confidence is down, too, raising the spectre of reduced demand.
Could part of the answer lie in improved business systems, reducing dependence on human effort, driving up efficiency in goods handling, and reducing the total cost of production? We’ll make the case in this blog.
Recently, the Employers and Manufacturers Association (EMA) noted that 100 percent of its members responding to a survey were struggling to fill vacancies. Nearly 40 percent had positions open for more than six months. The problems aren’t limited to government Covid restrictions, either. According to the EMA, the quality of applicants is poor not only in terms of skills but also in attitude and reliability. Read the full press release here (it is sobering reading, to be sure). An even more recent report in the Herald (paywalled) confirms what many already know: Manufacturing is contracting.
Is automation the answer?
These are precisely the sort of problems that drive employers of any kind, and manufacturers in particular, towards mechanisation and a reduction in dependence on human resources. After all, machines or software that get things done don’t complain, never request leave, don’t take Covid tests or require Covid furlough, and rock around the clock.
That is of course only one side of the equation. We’ve always known that you can’t replace people with machines or software in their totality. In fact, the notion of machines driving people out of work has a long history easily disproving the theory that this happens in any way. Back in the time of James Arkwright and his spinning frame, and the rise of the infamous Luddites, the idea was that people would be thrown out of work; the gains in efficiency actually meant more stockings for all at more affordable prices, as well as a net gain in employment.
The same issues were later traversed by notable economists including Henry Hazlitt in 1946 and Thomas Sowell in more recent times.
Yet another aspect is that gains in mechanisation or automation come at a not-insignificant cost. This most certainly applies to enterprise resource planning software like Oracle’s NetSuite – which we provide, support, and strongly advocate for manufacturers with diminishing avenues available for improving productivity and efficiency. As always, while a lot of the sums and the economics behind an ERP investment decision are necessarily complex, it comes down to a fairly simple question: is the juice worth the squeeze? The final calculation is just one of ‘will it be worth it’.
This isn’t easily answered and must be tackled on a case-by-case basis because most manufacturing concerns are complex businesses with complex software requirements.
But a broad case can be made, after which I welcome you to get in touch so we can assess your individual circumstances and establish if a shift to NetSuite cloud ERP might be right for your concern.
The case for NetSuite
NetSuite is one of the original cloud ERP solutions for small to medium-sized businesses, so it has a long history of successful implementations, from the ‘pioneering’ days when putting anything in the cloud was considered crazy, to present day where not putting things in the cloud is the exception rather than the rule.
At a basic level, NetSuite delivers all the stuff you’d expect for any business: an integrated ERP system including ERP, financials, commerce, inventory management, HR, PSA, supply chain management, CRM, and more.
The really good stuff for manufacturers is in NetSuite managing, coordinating, and automating complex business processes including engineering, planning, forecasting, procurement, manufacturing, supply chain, order management, warranty, and repairs, after-sales support and product data management. Read more here.
While many of these processes aren’t directly ‘factory floor’, a modern system nevertheless should integrate with your SCADA and PLC environments. When they do, your manufacturing concern benefits from improved production accuracy, reduced administration (and administrative staff – so you can focus on getting the skills that actually make things, rather than support personnel), and drives down inventory for improved cost control. A further advantage is available through integration with suppliers and customers, again improving efficiency and bringing to bear the concept of ‘Just In Time’ manufacturing, reducing ‘gaps’ in manufacturing to order, and efficiency gains across the supply chain.
As a cloud solution, the cost of introducing NetSuite may come as a (pleasant-ish) surprise. We’re not going to kid you and say it is cheap, nor will we claim it is simple, even with the proven SuiteSuccess implementation methodology (and our own track record, which we’re proud to have earned).
ERP is hard; again, though, it comes down to value against cost. And if the numbers stack up, there’s an excellent reason to consider an upgrade to one of the finest software solutions available today.
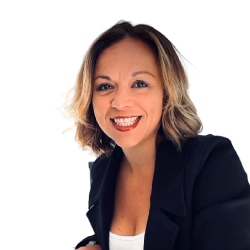