Selecting the right Enterprise Resource Planning (ERP) system is crucial for manufacturing businesses aiming to enhance efficiency, streamline operations, and drive growth. This blog outlines key considerations and steps to guide manufacturers in choosing an ERP solution that aligns with their specific needs and objectives.
Learn what factors to consider when selecting an ERP system for your manufacturing business.
12 Essential Questions to Pose to ERP Vendors
Every manufacturer has distinct requirements, yet there are some key considerations and inquiries you should present to an enterprise resource planning (ERP) vendor during the selection process:
- System Costs: What is the vendor's pricing structure for the ERP system we need now and for future capabilities? How are upgrades, new releases, and bug fixes managed?
- Implementation: What is the anticipated cost for implementation? How might that cost escalate once the project is in progress? How can we avoid scope creep?
- Manufacturing Expertise: Does the vendor provide functionality tailored to our specific manufacturing needs, such as production planning, inventory and supply chain management, demand and order management, and mobile shop floor control?
- Configurability: Does the vendor comprehend our specific needs and processes, and is the system adaptable enough to support them without extensive custom coding? How does the vendor's implementation team handle configurations?
- Integration: Does the ERP system integrate effectively with other core manufacturing systems to streamline data entry, enhance accuracy, and increase transparency? For instance, can it integrate with computer-aided design (CAD) applications to simplify costing or connect seamlessly with logistics providers for improved order management?
- User-Friendliness: Is the system easy to learn and use? Does it feature an intuitive user interface (UI) that will promote widespread adoption across our company? Global
- Capabilities: Does the system provide multilanguage and multicurrency capabilities to support our global supply chain, processes, and cross-border transactions?
- Timeline: How long will the implementation take? Will it disrupt our operations? How has implementation proceeded for other manufacturing customers? What resources will our company need to provide?
- Project Management: Will the vendor assist in creating milestones for success relevant to our business, such as improved cycle time, throughput, inventory turns, or costs per unit, ensuring everyone sees progress?
- Updates: How and how often does the vendor deliver software updates? Do new features incur additional costs? Do updates require expert assistance to install?
- Data Migration: How will the vendor assist in transferring data from old manufacturing systems to the new ERP? Does the provider have experience with our existing systems?
- Add-Ons: Does the vendor offer a variety of modules we can add as needed? Does it have an extensive network of partners offering prebuilt integrations and manufacturing functionality? How easy is it to add users or new functionality?
Key ERP Capabilities: What features are essential for your business?
- Accounting: Streamline accounts payable and receivable (AP/AR) processes; automatically update the general ledger and subledgers with real-time transactions; enhance intercompany accounting and costing; simplify the financial close with automated allocations, currency management tools, and period locking.
- Financial Planning and Analysis: Predict future sales, expenses, and staffing needs; develop product budgets; project base, best, and worst-case scenarios; model what-if situations; fully integrate financial statements.
- Inventory Management: Monitor product movement throughout the supply chain; keep track of current inventory levels and automatically trigger restocking alerts and reorder forms; incorporate demand planning forecasts to anticipate required inventory levels based on historical data, sales forecasts, open opportunities, and seasonal trends.
- Supply Chain Management: Evaluate supplier performance and outsourced manufacturing processes; facilitate data sharing with trade partners across the network; implement distribution requirement planning (DRP) capabilities for multilocation planning and automated generation of purchase orders, work orders, and transfer orders; provide real-time insights into supply chain management and spending metrics.
- Production Planning and Scheduling: Automatically balance supply to meet demand forecasts and actuals; develop and visualise production schedules; monitor production in real-time; identify and resolve potential scheduling conflicts.
- Mobile Shop Floor Control: Oversee work queues on the shop floor with durable devices; accurately document activity at each stage of the manufacturing process.
- Engineering and Quality Management: Enhance product design and quality; establish and maintain inspection plans and pass/fail criteria; collect and report on results; improve bill-of-materials management.
- Order Management: Handle all orders within a single system; integrate order-to-cash processes; fulfill orders based on inventory availability and business rules; direct orders to the optimal fulfillment location; track orders from receipt to delivery.
- Fixed Assets Management: Oversee the entire manufacturing asset lifecycle; calculate and report on depreciating and non-depreciating assets; track equipment warranties; establish maintenance schedules.
- Customer Relationship Management (CRM): Document all interactions with customers, prospects, and partners; manage sales leads; execute marketing campaigns; enhance customer service and support case management; manage warranty returns and repairs; enable customer self-service.
- Environmental, Sustainability, and Governance (ESG) Reporting: Measure, report, and reduce your company’s carbon footprint by tracking Scope 1, 2, and 3 emissions, carbon credits and offsets, and other ESG data; ingest and integrate ESG data from suppliers; generate regular ESG reports.
ERP systems are designed with modularity, allowing you to begin with essential financial functions and expand by adding modules for other business areas as needed.
3 Strategies to Persuade Internal Doubters
When it's crucial to gain the support of key stakeholders, follow these steps to secure approval for the ERP system investment.
Understand the Purpose
Highlight the specific challenges and how an ERP system addresses them. Industry realities include supply chain disruptions like shipping delays, material shortages, rising costs, and fluctuating customer demand. Fragmented data, disconnected digital tools, and manual processes hinder the visibility and agility manufacturers need to effectively navigate a dynamic business landscape. A robust ERP system enables manufacturers to adapt to changes in supply and demand, foresee business opportunities and challenges, manage daily transactions and operations, and develop a cohesive strategy for long-term success. An ERP system with manufacturing-specific modules provides tools and best practices to enhance transparency throughout the supply chain, manage costs, improve efficiency, and maintain competitiveness.
Justify Your ERP Choice
Seek a solution that offers the necessary modules and capabilities for both current and future needs. For new implementations, a cloud-based ERP system is the ideal choice due to its security, scalability, and cost-effectiveness. Ensure you outline the total costs, including implementation and training. Rely on vendor references from existing customers in the manufacturing sector to alleviate concerns and emphasise the value.
Plan Your Implementation Strategy
Implementing an ERP in phases is less risky than a "big bang," all-at-once approach, though it may lead to a slower return on investment. Running legacy systems in parallel for a period may be beneficial, especially in a continuously operating manufacturing environment. Develop an implementation schedule that considers resource availability and uptime requirements.
In conclusion, selecting the right ERP system is a pivotal decision that can significantly impact your manufacturing business's efficiency and growth. By asking the right questions and understanding the essential capabilities, you can ensure that your chosen solution aligns with your unique needs and future goals. Remember, a well-implemented ERP system not only streamlines operations but also enhances decision-making and competitiveness in a rapidly evolving market.
If you're ready to take the next step in transforming your manufacturing processes, we invite you to get in touch with our team of experts. We're here to support you in navigating the complexities of ERP selection and implementation, ensuring a seamless transition to a more integrated and efficient future.
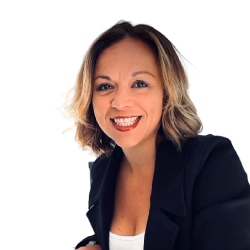